Click to watch Types of Requisitions video.
This section reviews the various types of requisitions in SpendMap and the workflow of each, including;
•Purchase Requisitions
•Item Requisitions
•Expense Reimbursement Requisitions
•Change Order Request
•Non-PO Invoice Request
•Invoice Discrepancy Request
All Requisition Types are Optional
You do not need to use all of these requisition types if you don't want to.
And even if you are using a particular type of requisition, you may not use it every time (i.e. for every purchase). While some SpendMap customers mandate the use of a requisition for everything (for maximum control), you may choose to forgo the online approval process for certain types of transactions, or for certain users. For example, even if most of your staff use Purchase Requisitions, there might be occasions where a Buyer or Purchasing Manager may create a Purchase Order from scratch in the PO Work Area (rather than building the PO from an approved Requisition), such as perhaps the renewal of yearly Blanket Orders, or perhaps orders to replenish stock don’t need approval in your company.
So even if you are using this module, you can pick and choose which types of requisitions you need to use and when, and you can still enter POs, Releases, RFQs, and inventory usages directly (i.e. without a requisition), as needed.
TIP: To prohibit users from entering POs or other transactions and force them to use Requisitions always, use User-Definable Menus to remove the applicable menu options for the PO Work Area or other document work areas that you don't want them to have access to.
Purchase Requisitions
Purchase Requisitions are used when the requisitioner wants to request that a specific Purchase Order be created.
Purchase Requisitions are almost identical to actual Purchase Orders, and may contain many or all of the details that will appear on the resulting Purchase Orders, such as the supplier, terms, item details, pricing, shipping instructions, etc. The difference is that the document has a requisition number rather than a PO number, and of course it may be routed for on-line approval before the goods or services are actually ordered.
If you're coming from a manual, paper-based environment, this is probably the type of requisition that you're used to. In fact, you may be using the same piece of paper to act as both a Requisition and an actual Purchase Order. But in SpendMap, we use the term "Purchase Requisition" for the document/transaction that is circulated internally for approval, while we reserve the term "Purchase Order" for the final/approved order that goes to the supplier.
Purchase Requisitions can be used in both a centralized and decentralized purchasing environment. In a decentralized purchasing environment where there is no central Purchasing Department, staff members might enter Purchase Requisitions for the products and services that they need, which can be routed for online approval before being converted/flipped into actual Purchase Orders to be sent to the suppliers. In this case, once the Requisitions are approved, they can be returned to the requisitioner as an official/approved PO to be sent to the supplier (i.e. the requisitioner processes the PO as well, as a separate step), or the PO can be sent directly to the supplier once it is approved using the No-Touch PO feature.
In a centralized purchasing environment (i.e. where there is a dedicated Buyer or Purchasing Department), once approved, Purchase Requisitions that were entered by end-user staff members can be sent to the Purchasing Department as official Purchase Orders, and the Buyers might review and possibly edit (e.g. clean up) the orders before sending them to the suppliers. Alternatively, a Buyer or Purchasing Agent might be the one to enter the Purchase Requisition if, for example, the Purchasing Manager or other Managers need to review/approve the order before the final PO is created.
NOTE: Unlike Item Requisitions that can split onto multiple POs, consolidated with other requisitions or routed to be filled from stock, a Purchase Requisition will remain intact and cannot be filled from stock. Again, the requisitioner is asking that a specific Purchase Order be created.
Workflow
This diagram outlines how Purchase Requisitions move from one step to the next...
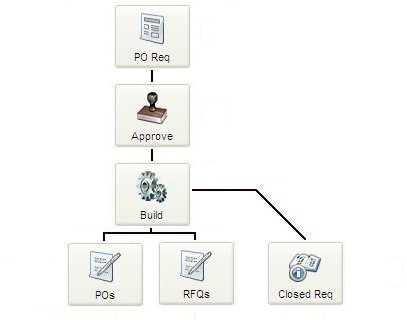
You can track the status of Purchase Requisitions as they move through the process using View Requisition Status up to the point that they are built into POs or RFQs. After that, you can track the status of the resulting PO or RFQ, with the applicable View Status utility (TIP: you can search for the PO or RFQ by the requisition number using Extended Lookup).
There are also various reports in the REPORTS section of the Main Menu that list requisition information.
Create Requisition
You can create new Purchase Requisitions in your Purchase Requisition Work Area.
If you are using the optional Inventory Control Module, you can include stock items on a Purchase Requisition. However, unlike with Item Requisitions, the item cannot come from stock (i.e. be filled from stock). A Purchase Requisition can, however, be used to request that stock items be purchased (i.e. to create a PO to replenish inventory).
Approval
Purchase Requisitions can be routed for on-line approval before being built into POs or RFQs. Please see Requisition Approval Routing for more details.
Build PO or RFQ
Once they are fully approved, Purchase Requisitions can be converted or "flipped" into POs or RFQs, with no duplicate data entry.
The resulting PO or RFQ documents can either be sent back to the Requisitioner, or sent to a Buyer to work on, or sent directly to suppliers electronically.
Document Work Areas
Other than POs that are sent directly to suppliers as part of the document build process (see No-Touch POs), the build process will send documents to the applicable user’s PO Work Area or RFQ Work Area.
Depending on how your system is configured and the options that you are using, a single build operation may result in documents being routed to one or more users.
You can optionally use automatic notifications to let users know that they have new documents to work on.
Closed Requisition Log
When Purchase Reqs are built into POs or RFQs, the details of each requisition are also stored in the Closed Req Log for reference purposes.
In the Log, you can see the details of each req, who approved each item and when, and the resulting document that each req was built into.
|
Item Requisitions
Item Requisition are popular for “end-user” requisitioning (i.e. when staff members need products or services for their own use), mainly because of their versatility and simplicity. A single Item Requisition can include both stock and non-stock items, items in the Item Master File as well as one-off (free-form) items, and can also include items from different suppliers on the same requisition.
Without worrying about where the items will come from, your staff will simply request the items that they need and SpendMap will take care of the rest, sending the requisition to the right people for approval before routing inventory items to the Stock Room to be filled (if you're using the optional Inventory Control Module), and creating one or more Purchase Orders for whatever needs to be ordered from suppliers.
Item Requisitions are often used in a centralized purchasing environment, where a separate Buyer or Purchasing Department interacts with the suppliers rather than the end-user requisitioners themselves.
You can create Item Requisitions in the Item Requisition Work Area or the Item Requisition Shopping Cart.
Mobile Web App
You can also create Item Requisitions using your Smartphone or tablet in the Mobile Web App.
|
Workflow
This diagram outlines how Item Requisitions move from one step to the next...
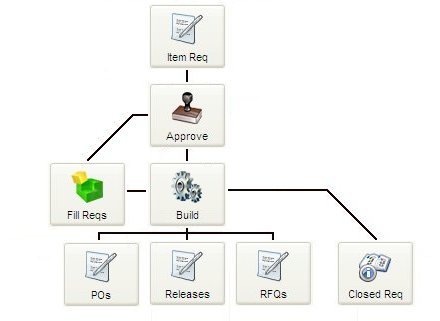
You can track the status of Item Requisitions as they move through the process using View Requisition Status up to the point that they are filled from stock or built into POs or other documents. After that, you can track the status of the resulting PO, Release or RFQ with the applicable View Status utility (TIP: you can search for the PO, Release or RFQ by the requisition number using Extended Lookup).
There are also various reports in the REPORTS section of the Main Menu that list requisition information.
Create Requisition
You can create Item Requisitions in the Item Requisition Work Area or the Item Requisition Shopping Cart.
If you are using the optional Inventory Control Module, Item Reqs can be used to request items from stock. When an Item Requisition is created for a stock item in the Item Master File, SpendMap will automatically reserve the stock until the requisitions are approved and filled from stock.
Approval
Item Requisitions can be routed for on-line approval before being filled from stock or built into POs or other procurement documents. Please see Requisition Approval Routing for more details.
Stock Room (fill from consumable inventory)
If you are using the optional Inventory Control Module, Item Requisitions for items that are being maintained in stock, once approved, can be filled from stock rather than built into POs or other procurement documents.
Stock items that cannot be filled from stock (i.e. if there is a stock-out) may be routed to create procurement documents or may simply be back-ordered pending receipt of additional inventory, at which time the reqs can be filled.
If you are using the Inventory Control Module but prefer to bypass the Stock Room and create POs or other procurement documents for ALL Item Requisitions (even reqs for stock items), use the setting called “Bypass stock room...” in Misc. Requisition Settings.
Build Procurement Documents
Once they are approved, Item Requisitions (that are not filled from stock, per above) can be converted or "flipped" into procurement documents (POs, Releases or RFQs), with no duplicate data entry.
The resulting documents can either be sent back to the Requisitioner, or sent to a Buyer to work on, or sent directly to suppliers electronically.
Item Reqs can optionally be split onto multiple POs or other documents (e.g. if they contain items from multiple suppliers) and/or consolidated with other Item Reqs to save shipping costs.
Creating a Purchase Req from and Item Req
An Item Requisition, once approved, can also be turned into a Purchase Requisition and then sent for a separate round of approval.
Some organizations use two rounds of approval. This is most common where end-user Requisitioners request items to be sourced by a central Purchasing group.
In environments like this, end-user Requisitioners might use Item Requisitions to ask for what they need but without specifying all the details, like the supplier or even pricing.
These item Requests can then be routed to the central Purchasing group to source, obtain pricing, etc., at which point the missing details can be filled in and then a (complete) Purchase Requisitions can be created and forwarded through a final approval process.
Related setting: If approval is only needed for the final (complete) Purchase Requisition but not the original Item Request, you can bypass approvals for Item Reqs using the “Approvals for item requisitions” setting in Misc. Approval Rules and Settings.
|
Document Work Areas
Other than POs that are sent directly to suppliers as part of the document build process (see No-Touch POs), the build process will send documents to the applicable user’s PO Work Area, Release Work Area and/or RFQ Work Area.
Depending on how your system is configured and the options you are using, a single build operation may result in the creation of multiple document types, with documents being routed to one or more users.
You can optionally use automatic notifications to let users know that they have new documents to work on.
Closed Requisition Log
When Item Reqs are either filled from stock or built into POs or other procurement documents, the details of each requisition are also stored in the Closed Req Log for reference purposes.
In the Log, you can see the details of each req, who approved each item and when, and the resulting document that each req was built into.
|
Expense Reimbursement Requisitions
Expense Reimbursement Requisitions are used when someone needs to be paid back for something that they bought with their own money.
Companies usually spend money in two ways; either they process Purchase Orders and pay supplier invoices, or employees just spend their own money and expense it later.
With Expense Reimbursement Requisitions (sometimes called Expense Management, Expense Reporting, Travel and Expense, or T&E), you can replace your paper or Excel-based "expense sheets", to reduce paperwork, accelerate the approval process, and simplify reporting for employee expense reimbursements.
Much like Purchase Reqs and Item Reqs, Expense Reimbursement Reqs can be routed for online approval to ensure that proper approval is obtained for every expense. However, once an Expense Reimbursement Request is approved, SpendMap will simply send a "check request" to your Accounting, ERP or Payroll system to process a payment to the applicable staff member, rather than creating a new Purchase Order, since the end-user has already purchased and paid for the items in question.
In addition to eliminating paperwork and accelerating the approval process, approved Expense Reimbursement Requests will update spending history, Cost Center budgets, the executive dashboards, and many other areas of SpendMap, allowing you to capture and report on all non-payroll spending in one place.
Workflow
This diagram outlines how Expense Reimbursement Requisitions move from one step to the next...
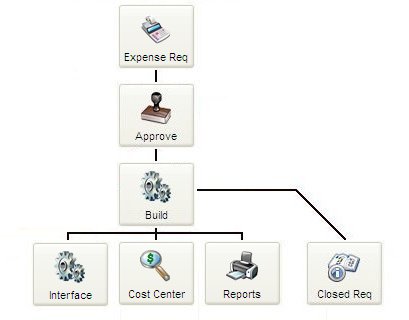
You can track the status of Expense Requisitions as they move through the process using View Requisition Status up to the point that they are fully approved, after which the details will be available in the Closed Requisition Log and the other areas/reports that are updated with Expense history (see below for details).
There are also various reports in the REPORTS section of the Main Menu that list requisition information.
Create Requisition
You can create new Expense Requisitions in your Expense Reimbursement Requisition Work Area.
Approval
Expense Requisitions can be routed for on-line approval before issuing payment to the end-user. Please see Requisition Approval Routing for more details.
Expense Reqs can either follow the same approval routing as other types of Requisitions (i.e. based on the same business rules, etc.) or you can assign special/different approval levels for Expense Reqs, in Miscellaneous Approval Rules and Settings.
You can optionally use automatic notifications to let users know that their Expense Reqs were approved.
Build
Once they are fully approved, Expense Reimbursement Requisitions will be posted to various areas in SpendMap (see below). This will happen automatically when the last approver approves the Requisition.
However, in some cases, you must run the document building process to complete this posting (e.g. if no approval is required for Expense Reqs).
Accounting Interface
SpendMap can send a "check request" to your Accounting, ERP or Payroll system to process a payment to the requisitioner.
There are two options for exporting the payment details for processing by another system. If you are using SpendMap's Invoice Approval Module, approved Expense Reqs can be exported as a separate transaction "type", along with approved Invoices, using the the Approved Invoice Export. That is, a single export can include both approved invoice transactions and expense reimbursement transactions. This assumes that your Accounting System can parse/separate the different transaction types as they are imported (e.g. invoices payments go to suppliers, while expense reimbursement payment go to employees).
Alternatively, a separate/dedicated Expense Reimbursement Export is also provided, which can be enabled with the setting called "Use separate interface for expense reimbursements" in A/P Interface Settings.
Cost Center History, Budgets and Other Reports
Approved Expense Reimbursement Requisitions will update the applicable Cost Center's history and budget status, so that you can get a complete view into your expenditures, regardless of how the money was actually spent.
Approved Expense Reqs will also update the Tax/Audit Trail Report, as well as other related reports that pull data from the Tax/Audit Trail table, including the Supplier Spend by Date Range Report (assuming that the supplier was indicated on the Expense Reqs, which is optional).
Finally, various Dashboard KPIs are updated with the details of Expense Reimbursement Requisitions as well.
Closed Requisition Log
When Expense Reimbursement Reqs are approved and processed, the details of each requisition will be stored in the Closed Req Log for reference purposes, including any attachments (e.g. scanned receipts).
|
Change Order Requests (auto-created by SpendMap)
If you are using the Advanced PO Modification Utility, you can optionally route Change Orders for on-line approval before they are processed.
This feature can be enabled and customized with the setting called "PO change order processing options", in PO Processing Settings.
If enabled, when a Change Order is processed using the Advanced PO Modification Utility, SpendMap will automatically create an Item Requisition with the details of the changes, and the Change Order will remain “on hold” in the Buyer’s PO Work Area until the Requisition is approved, at which point the Change Order will be “released” and can be processed by the Buyer as usual.
A corresponding e-mail notification called “Approved or rejected PO change orders” is available to inform the Buyer when the Change Order is approved and ready for processing.
Non-PO Invoice Request (auto-created by SpendMap)
If you are using Non-PO Invoices, they can optionally be routed for on-line approval before being processed.
One of the options for online approval of Non-PO Invoices is to route them through the Requisitions and Approvals Module. This feature can be enabled and customized with the setting called "Non-PO invoice processing options", in Invoice Options.
If enabled, when a Non-PO Invoice is entered, SpendMap will automatically create an Item Requisition with the details of the invoice, and the invoice will remain “on hold” in the user's Invoice Work Area until it is approved. Once approved, the invoice will either be processed immediately or will be “released” and returned to the original user for final processing.
Non-PO Invoices Reqs can either follow the same approval routing as other types of Requisitions (i.e. based on the same business rules, etc.) or you can assign special/different approval levels for Invoices, in Miscellaneous Approval Rules and Settings.
For more details and additional options, please see "Invoice Approval Routing", in Types of Invoices and Workflow.
Invoice Discrepancy Request (auto-created by SpendMap)
If you are using the Invoice Discrepancy feature, invoice discrepancies can optionally be routed for on-line approval before being processed.
One of the options for online approval of invoice discrepancies is to route them through the Requisitions and Approvals Module. This feature can be enabled and customized with the setting called "Invoice discrepancy approval/routing options", in Invoice Options.
If enabled, when an invoice discrepancie occurs, SpendMap will automatically create an Item Requisition with the details of the invoice, and the invoice will remain “on hold” in the user's Invoice Work Area until it is approved. Once approved, the invoice will either be processed immediately or will be “released” and returned to the original user for final processing.
Invoices Discrepancy Reqs can either follow the same approval routing as other types of Requisitions (i.e. based on the same business rules, etc.) or you can assign special/different approval levels for Invoices, in Miscellaneous Approval Rules and Settings.
For more details and additional options, please see "Invoice Approval Routing", in Types of Invoices and Workflow.